Ordering Process
At Optimax, we manufacture high-precision optics for a range of applications, providing a superior customer service experience. We are committed to building the future by cultivating critical partnerships with optical engineers and key decision-makers across the full spectrum of optical engineering and design. If you would like to talk through the ordering process, contact a member of the Optimax team directly.
Inspection Data Options
We inspect all manufactured optical components 100%. Three options—outlined here—are available for providing data packets electronically. When placing an order, please consider which option best suits your project.
Complying with manufacturing standards issued by:
- STANDARD
- ENHANCED
- LASER DAMAGE
Verification Data Package includes:
Verification Data Package includes:
- Certificate of Conformance
- Serialization
- 100% recorded values for all physical dimensions
- Inspection Data Record
- Melt Data
- Coating Curves (if applicable)
Verification Data Package Options: (Choose One):
Customer-defined test plan or à la carte inspection options available include:
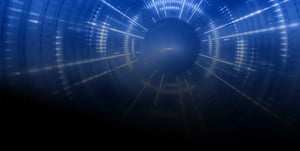
Have Additional Questions?
Contact a sales engineer for further information.
Packaging Options
Optimax cleans and wraps each optic to protect it from mechanical and chemical (staining) damage and desiccant will be added when necessary to protect the lenses from staining. The optics are then wrapped and packed into a protective shipping box.
If interested, you may select non-contact or clean-room packaging.
Standard: Cotton Bag
- Size: Lenses 15mm – 80mm in diameter
- Cleanliness: Class 10,000
- Packaging: Lenses are wrapped in lint-free rayon sheets and then placed in cotton bags.
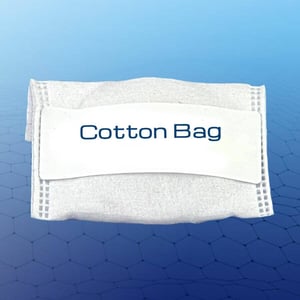
Standard: Lens Paper/Bubble Wrap
- Size: Lenses larger than 80mm in diameter
- Cleanliness: Class 10,000
- Packaging #1: Lenses are wrapped in lint-free rayon sheets and then lens paper.
- Packaging #2: They are then placed in bubble wrap pouches in plastic bags.
* Gel capsules are available upon request for optics smaller than 15mm in diameter.

Non Contact: PETG
- Size: Recommended for lenses between 100-300+mm in diameter
- Cleanliness: Class 1,000
- Packaging: Lenses are placed in PETG containers which avoid contact with the optical surfaces by only contacting the edges.
* Additional cost
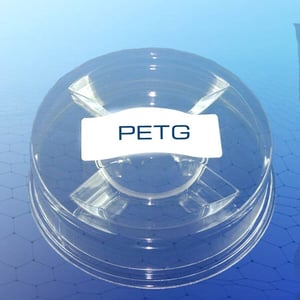
Clean Room
- Cleanliness: Class 100
- Packaging #1: Lenses are placed in clean-room sanitized containers that do not make contact with lens surfaces.
- Packaging #2: Containers are then placed in 2-layers of polymer bags that are sealed within the cleanroom.
* Additional cost
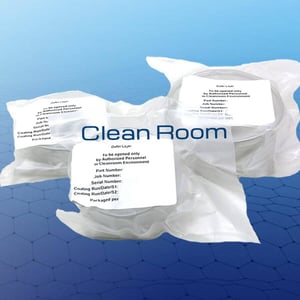
Corporate & Compliance Information
Optimax operates under both our Business and Vendor Terms and Conditions. To ensure you receive the correct documentation, please review the terms below and explore other useful documents in our library that may assist with the ordering process.
W9
Optimax’s current W-9 form detailing our Taxpayer Identification Number (TIN).
Learn MoreVendor Terms and Conditions
These Vendor Terms and Conditions, together with the accompanying Optimax Systems, Inc. (Optimax) purchase order, constitute the terms and conditions for the Contract between Optimax and Seller.
Optimax Quality Manual
Our quality manual details policies that allow us to achieve high-quality products that meet customers’ and ISO’s requirements.
Learn MoreNon-Disclosure Agreement (Mutual)
This is Optimax’s Standard Mutual Non-Disclosure Agreement in an editable template format.
Learn MoreFinancial Disclosure Policy
This is Optimax's Financial Disclosure Policy.
Learn MoreCorporate Information
Optimax’s General Corporate Information, such as our mailing address, TIN, D&B#, building info, etc., can be found here.
Learn MoreCompany Profile
Optimax's reliability has allowed us to become America's largest optics prototype manufacturer. Find the full company profile and details here.
Learn MoreConditions of Sale (Terms & Conditions)
This document constitutes the Terms and Conditions under which Optimax will manufacture optical products for the customer unless superseded by another agreement.
LEARN MORERoHS, REACH, Conflict Materials Statement
Optimax’s compliance policies are detailed within this document.
LEARN MOREISO 9001:2015 Certificate of Registration
Optimax’s Quality Management System complies with ISO9001:2015.
LEARN MORENIST SP800-171 (DoD) Cyber Security Compliance Statement
Optimax’s compliance policy is detailed within this document.
LEARN MOREMilitary Specifications MIL-C-675C
This specification establishes the durability and abrasion resistance requirements of anti-reflection interference films used on optical materials.
LEARN MOREDefense Logistics Agency
Optimax is certified by the Defense Logistics Agency. Download PDF for certification verification.
LEARN MOREDDTC Registration
Optimax is registered with the Directorate of Defense Trade Controls (DDTC). Download certificate.
LEARN MOREEthics, Code of Conduct, HSE Statement
Optimax’s compliance policies are detailed within this document.
LEARN MOREExpedited Delivery
If expedited delivery is requested at the time of order, our team will assess our ability to meet the delivery. This includes verifying the availability of optical materials, workforce availability, and technical requirements.
Optimax provides an On-Time Guarantee. We work hard, but we’re not perfect, so any unearned premium will be refunded to the customer in the event of late delivery.
Contact our sales team to learn more about expedited deliveries:
ADDRESS: 6367 Dean Parkway
Ontario, NY 14519
PHONE: (585) 265-1020
EMAIL: sales@optimaxsi.com
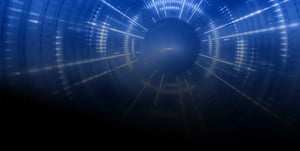
Would you like to find out more?
With a deep understanding of diverse optical challenges, Optimax offers tailored solutions through a combination of traditional and advanced CNC machining. Explore our precision optics, opto-mechanical assemblies, and optical systems design expertise, serving industries like aerospace and semiconductor.